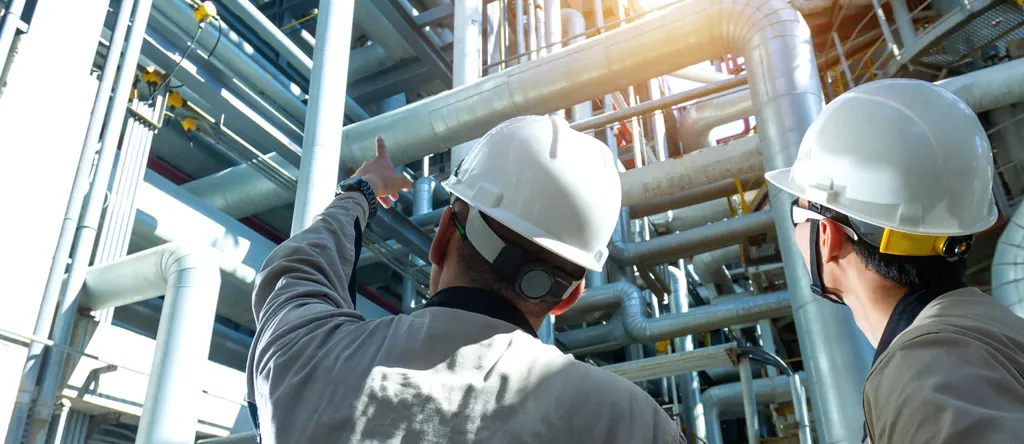
Mantenimiento Predictivo Industrial: Ventajas y Herramientas Clave
El mantenimiento predictivo industrial se ha convertido en una de las estrategias más efectivas para garantizar el funcionamiento continuo y eficiente de equipos industriales. A diferencia del mantenimiento correctivo, que actúa después de una falla, o del mantenimiento preventivo, que se realiza de manera regular, el mantenimiento predictivo permite prever fallas antes de que ocurran, optimizando tanto los tiempos de operación como los recursos. En este artículo, exploraremos las ventajas del mantenimiento predictivo y las herramientas clave que lo hacen posible.
¿Qué es el Mantenimiento Predictivo?
El mantenimiento predictivo es una estrategia de mantenimiento basada en la monitorización continua o periódica del estado de los equipos y sistemas mediante el uso de tecnologías avanzadas. El objetivo es detectar posibles fallos o desgastes en sus primeras etapas, permitiendo intervenir antes de que se produzca una avería. Este tipo de mantenimiento se apoya en datos reales obtenidos a través de sensores y dispositivos de diagnóstico, lo que permite realizar un análisis detallado y tomar decisiones informadas.
Ventajas del Mantenimiento Predictivo
El mantenimiento predictivo ofrece múltiples ventajas que lo hacen indispensable en entornos industriales modernos. A continuación, se detallan algunas de las más significativas:
1. Reducción de Tiempos de Inactividad
Una de las principales ventajas del mantenimiento predictivo es la significativa reducción de tiempos de inactividad no planificados. Al identificar problemas potenciales antes de que provoquen fallas, se pueden programar reparaciones en momentos que no interfieran con la producción, minimizando así el impacto en la operación general.
2. Extensión de la Vida Útil de los Equipos
El monitoreo continuo del estado de los equipos permite identificar patrones de desgaste y deterioro, lo que facilita la implementación de medidas correctivas antes de que se produzca un daño irreversible. Esto extiende la vida útil de los equipos, asegurando que funcionen de manera óptima durante más tiempo.
3. Optimización de Costos
El mantenimiento predictivo contribuye a una optimización significativa de los costos. Aunque la implementación inicial de este tipo de mantenimiento puede requerir una inversión en tecnología y capacitación, los ahorros a largo plazo en reparaciones costosas, tiempos de inactividad y reemplazo de equipos compensan con creces esta inversión.
4. Mejora de la Seguridad
Al prever fallas y evitar averías inesperadas, el mantenimiento predictivo también mejora la seguridad en el lugar de trabajo. Los equipos que operan en condiciones óptimas tienen menos probabilidades de causar accidentes, lo que protege tanto a los trabajadores como a la infraestructura.
5. Aumento de la Eficiencia Operativa
Con el mantenimiento predictivo, las empresas pueden planificar de manera más eficiente sus operaciones, evitando interrupciones inesperadas y asegurando que los recursos estén disponibles cuando se necesitan. Esto resulta en una mayor eficiencia y productividad en las líneas de producción.
Herramientas Clave para el Mantenimiento Predictivo
El éxito del mantenimiento predictivo depende en gran medida de las herramientas y tecnologías utilizadas para recopilar y analizar datos. A continuación, se presentan algunas de las herramientas clave:
1. Sensores de Vibración
Los sensores de vibración son esenciales para monitorear el estado de equipos rotativos, como motores, compresores y bombas. Estos sensores detectan cambios en los patrones de vibración, que pueden indicar problemas como desalineación, desbalanceo, o desgaste en los rodamientos. Los datos de vibración permiten identificar problemas en sus primeras etapas, facilitando intervenciones oportunas.
2. Termografía Infrarroja
La termografía infrarroja es una herramienta que utiliza cámaras térmicas para detectar puntos calientes en equipos eléctricos y mecánicos. Estos puntos calientes pueden ser indicativos de conexiones sueltas, sobrecalentamiento, o fricción excesiva, problemas que, si no se abordan, podrían llevar a fallos graves.
3. Análisis de Aceite
El análisis de aceite es una técnica utilizada para evaluar el estado de lubricantes en equipos mecánicos. A través de este análisis, es posible detectar contaminantes, desgaste de componentes internos, y otros problemas que podrían no ser visibles de otra manera. Esto permite intervenir antes de que el problema se agrave.
4. Ultrasonido
El ultrasonido es una herramienta utilizada para detectar fugas de aire, gas o vapor en sistemas de presión, así como para identificar problemas en rodamientos y componentes eléctricos. La tecnología de ultrasonido es altamente sensible y puede identificar problemas antes de que sean detectables por otros medios.
5. Análisis de Corriente
El análisis de corriente se utiliza principalmente en motores eléctricos para detectar problemas como sobrecarga, desbalanceo y otros fallos eléctricos. Esta herramienta ayuda a prevenir fallos mayores y a optimizar el rendimiento del motor.
6. Monitoreo de Condición en Tiempo Real (IoT)
El Internet de las Cosas (IoT) ha revolucionado el mantenimiento predictivo al permitir el monitoreo de condición en tiempo real. Los sensores conectados a la red recopilan datos continuamente, los cuales son analizados mediante algoritmos avanzados de machine learning para detectar patrones de fallos. Esta tecnología permite intervenciones mucho más precisas y oportunas.
Implementación del Mantenimiento Predictivo Industrial
Implementar un programa de mantenimiento predictivo requiere una planificación cuidadosa. Es fundamental contar con el personal capacitado y con las herramientas adecuadas. Además, es importante establecer una estrategia de recopilación y análisis de datos que permita obtener información precisa y accionable.
Las empresas que invierten en mantenimiento predictivo deben estar dispuestas a adoptar una mentalidad orientada a la innovación y la mejora continua. La integración de nuevas tecnologías y la capacitación continua del personal son esenciales para maximizar los beneficios de esta estrategia.
Conclusión
El mantenimiento predictivo industrial representa una de las estrategias más efectivas para mejorar la eficiencia, reducir costos y aumentar la vida útil de los equipos en entornos industriales. Su capacidad para prever fallas antes de que ocurran y permitir intervenciones programadas lo convierte en una herramienta indispensable para cualquier empresa que busque optimizar sus operaciones.
Adoptar el mantenimiento predictivo no solo implica una inversión en tecnología, sino también un cambio en la forma en que se gestionan los activos. Sin embargo, los beneficios a largo plazo, tanto en términos de ahorro de costos como en la mejora de la seguridad y la eficiencia, hacen que esta estrategia sea una opción altamente recomendable para las empresas que buscan mantenerse competitivas en un entorno industrial cada vez más exigente.
Visita los siguientes enlaces si quieres conocer más sobre el mantenimiento predictivo:
https://es.wikipedia.org/wiki/Mantenimiento_predictivo
https://blog.infraspeak.com/es/mantenimiento-predictivo/