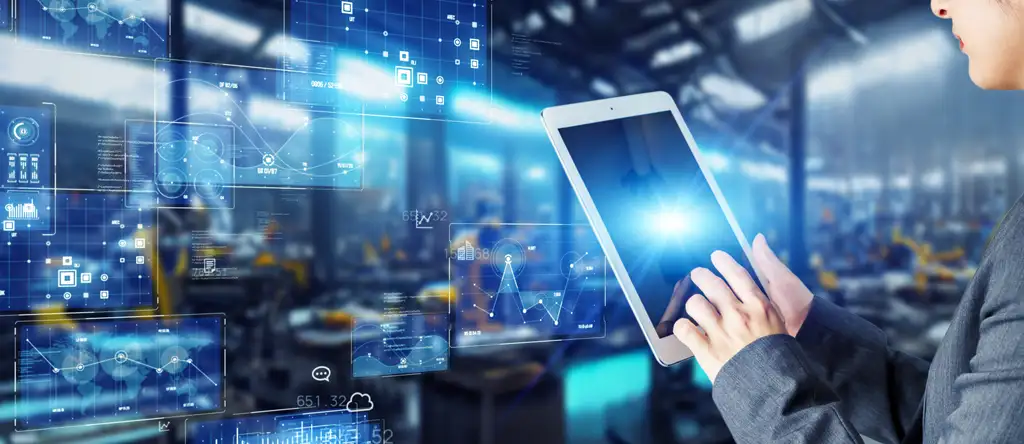
Detección de Fallos en Tiempo Real: Tecnología y Beneficios
En el entorno industrial actual, donde la eficiencia y la continuidad operativa son esenciales, la detección de fallos en tiempo real se ha convertido en una tecnología clave para garantizar que los equipos y sistemas funcionen sin interrupciones. Esta capacidad de identificar problemas en el momento en que ocurren, o incluso antes, permite a las empresas tomar medidas preventivas, minimizar tiempos de inactividad y optimizar sus procesos. En este artículo, exploraremos las tecnologías que hacen posible la detección de fallos en tiempo real y los beneficios que ofrece para las operaciones industriales.
1. ¿Qué es la Detección de Fallos en Tiempo Real?
La detección de fallos en tiempo real es la capacidad de monitorear continuamente el estado de los equipos y sistemas para identificar anomalías o problemas tan pronto como ocurren. Esto se logra mediante el uso de sensores, algoritmos de análisis de datos y sistemas de alerta que permiten a los operadores tomar decisiones inmediatas para corregir problemas y evitar fallos graves.
Monitoreo Continuo y Análisis Inmediato
A diferencia de los métodos tradicionales de inspección y mantenimiento, que suelen basarse en revisiones periódicas, la detección en tiempo real permite un monitoreo continuo. Los datos recopilados por sensores se analizan al instante, lo que permite identificar patrones anómalos y activar alertas en tiempo real.
2. Tecnologías para la Detección de Fallos en Tiempo Real
Existen varias tecnologías clave que permiten la detección de fallos en tiempo real. Estas tecnologías han avanzado significativamente en los últimos años, impulsadas por el desarrollo del Internet de las Cosas (IoT), la inteligencia artificial (IA) y la conectividad avanzada.
1. Sensores IoT
Los sensores IoT son fundamentales para la detección en tiempo real, ya que permiten monitorear diversas variables críticas, como temperatura, vibración, presión, flujo de corriente y más. Estos sensores recopilan datos de manera continua y los transmiten a un sistema central para su análisis.
2. Análisis de Vibraciones
El análisis de vibraciones es una técnica ampliamente utilizada para detectar fallos en equipos rotativos, como motores, bombas y compresores. Los sensores de vibración detectan cambios en los patrones de vibración que pueden indicar problemas como desalineación, desgaste de rodamientos o desbalanceo. Este tipo de análisis permite identificar fallos antes de que causen daños graves.
3. Termografía Infrarroja
La termografía infrarroja utiliza cámaras térmicas para detectar variaciones de temperatura en los equipos. Estas variaciones pueden ser indicativas de problemas como sobrecalentamiento, fricción excesiva o fallos en sistemas eléctricos. La termografía es especialmente útil para monitorear motores eléctricos, tableros de distribución y sistemas de refrigeración.
4. Análisis de Fluidos
El análisis de fluidos, como el análisis de aceite en motores y sistemas hidráulicos, permite detectar contaminantes y partículas de desgaste que podrían indicar un fallo inminente. Esta tecnología es crucial para prever problemas en sistemas que dependen de la lubricación para su funcionamiento.
5. Inteligencia Artificial y Machine Learning
La inteligencia artificial (IA) y el machine learning están revolucionando la detección de fallos en tiempo real. Estas tecnologías permiten analizar grandes volúmenes de datos en busca de patrones complejos que podrían pasar desapercibidos para los humanos. Los algoritmos de machine learning pueden aprender de datos históricos y ajustar sus predicciones para mejorar la precisión de la detección.
3. Beneficios de la Detección de Fallos en Tiempo Real
La implementación de tecnologías de detección de fallos en tiempo real ofrece una serie de beneficios significativos para las empresas industriales.
1. Reducción de Tiempos de Inactividad
El beneficio más evidente de la detección de fallos en tiempo real es la reducción de los tiempos de inactividad no planificados. Al identificar y corregir problemas antes de que causen fallos catastróficos, las empresas pueden mantener sus operaciones en funcionamiento continuo, lo que se traduce en una mayor productividad y menores pérdidas económicas.
2. Aumento de la Vida Útil de los Equipos
La capacidad de detectar problemas en sus etapas iniciales también contribuye a la prolongación de la vida útil de los equipos. Al realizar intervenciones de mantenimiento oportunas, se evita el desgaste excesivo y se asegura que los equipos operen dentro de sus parámetros óptimos durante más tiempo.
3. Optimización del Mantenimiento
La detección en tiempo real permite optimizar el mantenimiento mediante la implementación de un enfoque predictivo en lugar de reactivo. Esto significa que el mantenimiento se realiza solo cuando es necesario, lo que reduce los costos asociados con el mantenimiento preventivo excesivo y las reparaciones de emergencia.
4. Mejora en la Seguridad
La detección temprana de fallos también mejora la seguridad en el lugar de trabajo. Al prever fallos que podrían causar accidentes, como explosiones, fugas de sustancias peligrosas o fallos estructurales, se protege a los trabajadores y se minimizan los riesgos para la infraestructura de la planta.
5. Cumplimiento Normativo y Reducción de Sanciones
En industrias altamente reguladas, como la energética y la química, el cumplimiento de normativas de seguridad es crucial. La detección de fallos en tiempo real ayuda a asegurar que los equipos operen dentro de los parámetros permitidos, evitando sanciones y garantizando el cumplimiento de las normativas vigentes.
4. Implementación de la Detección de Fallos en Tiempo Real
Implementar un sistema de detección de fallos en tiempo real requiere una planificación cuidadosa y la selección de las tecnologías adecuadas. A continuación, se describen los pasos clave para una implementación exitosa.
1. Evaluación de Necesidades
El primer paso es evaluar las necesidades específicas de la planta o instalación. Esto implica identificar los equipos críticos, los tipos de fallos más comunes y las variables que deben monitorearse.
2. Selección de Tecnología
Una vez identificadas las necesidades, se deben seleccionar las tecnologías de detección más adecuadas. Es importante considerar factores como la compatibilidad con los sistemas existentes, la facilidad de integración y el costo total de propiedad.
3. Integración con Sistemas de Gestión
El sistema de detección de fallos en tiempo real debe integrarse con el Sistema de Gestión de Mantenimiento Computarizado (CMMS) para facilitar la planificación y ejecución de las tareas de mantenimiento. Esta integración permite que las alertas generadas por el sistema de detección se conviertan automáticamente en órdenes de trabajo.
4. Capacitación del Personal
Es crucial que el personal de mantenimiento esté capacitado en el uso de las nuevas tecnologías y en la interpretación de los datos generados por los sistemas de detección. Esto asegura que el equipo pueda reaccionar rápidamente ante las alertas y tomar decisiones informadas sobre las intervenciones necesarias.
5. Revisión y Mejora Continua
Finalmente, es importante revisar y mejorar continuamente el sistema de detección de fallos en tiempo real. Esto implica analizar el rendimiento del sistema, ajustar los parámetros de monitoreo según sea necesario y asegurarse de que el sistema evolucione con las necesidades cambiantes de la planta.
Conclusión
La detección de fallos en tiempo real es una herramienta poderosa para mejorar la eficiencia, la seguridad y la rentabilidad en el entorno industrial. Al aprovechar las tecnologías avanzadas disponibles, como sensores IoT, análisis de vibraciones, termografía infrarroja y machine learning, las empresas pueden anticipar problemas antes de que se conviertan en fallos graves. Esto no solo reduce los tiempos de inactividad y prolonga la vida útil de los equipos, sino que también optimiza los procesos de mantenimiento y mejora la seguridad operativa. En un mundo donde la competitividad y la eficiencia son clave, la detección de fallos en tiempo real es una inversión esencial para cualquier empresa industrial.